一、机组润滑和冷却系统的自动化
1.机组润滑和冷却系统的概况与控制要求
水轮发电机组一般设有推力轴承、上导轴承、下导轴承和水轮机导轴承。推力轴承和上、下导轴承采用30号稀油润滑的巴氏合金轴瓦(锡锑轴承合金、铅锑轴承合金统称巴氏合金、钨金或白合金),1990年以后也常采用弹性金属氟塑料瓦。水轮机导轴承有的采用稀油润滑的钨金瓦,有的则采用水润滑的橡胶轴瓦。机组运转时,巴氏合金轴瓦因摩擦产生的热量靠轴承内油冷却器的循环冷却水带走。采用橡胶轴瓦时,水不仅起润滑作用,同时也起冷却作用,由于结构上的不同,两种轴承对自动化控制亦有了不同的要求。
采用油润滑的巴氏合金轴瓦的轴承时,要求轴承内的油位保持一定高度,且轴瓦的温度不应超过规定的允许值,如不正常则应发出相应的故障信号或事故停机信号。冷却水中断时不要求立即停机,只需发故障信号,以通知运行人员进行处理。为了节约用水,冷却水在开机运转时才投入,其投入和切除由机组总冷却水电磁配压阀(带ZT电磁铁)控制,轴承冷却水不单独设操作阀。这部分的自动化比较简单。
采用水润滑的橡胶轴承时,即使润滑水短时间中断,也会引起轴瓦温度急剧升高,导致轴承的损坏,因此需要立即投入备用润滑水,并发出相应的信号。如果备用润滑水电磁配压阀(带ZT电磁铁)启动后仍无水流,则经过一定时间(例如3s)后应作用于事故停机。
对于低水头电厂(站)来说,若节约用水不那么重要,为简化操作控制和提高可靠性,可以采用经常性供给润滑水的方式,即不切除电磁阀。
除了轴承需要冷却水以外,发电机也需要带走运行时内部铜铁损所产生热量的冷却系统。发电机冷却方式一般有三种:其一是空气冷却方式,例如丹江口150MW机组采用密闭式自循环通风,借助循环于空气冷却器的冷风带出发电机内部产生的热量,而空气冷却器则靠内管冷却水进行冷却;其二是水内冷方式,例如三峡机组采用的冷却方式有半水内冷,经过处理的循环冷却水直接通人定子绕组的空心导线内部和铁心中的冷却水管,将运行时内部铜铁损产生的热量带走,控制系统应保证冷却水的供应和水质合格;其三是蒸发冷却,如李家峡400MW机组显示出蒸发冷却技术应用于大容量机组的优势。由于采用的冷却介质属于氟利昂类产品,所含氯元素对大气的臭氧层有破坏作用,目前限制使用F11、F12、F13。为了提高冷却效果,并出于保护环境的考虑,新型无毒、无污染的冷却介质将在实际机组中使用。
采用空气冷却方式时,空气冷却器的冷却水由机组总冷却水电磁阀供应,开机时打开总冷却水电磁阀,停机时关闭总冷却水电磁阀。用示流传感器进行监视,中断时发出故障信号,但不作用于事故停机。这部分比较简单。
采用水内冷却方式时,由于对冷却水的水质、水压、流量有严格要求,故需单独设置供水系统。短时间的冷却水中断可能导致发电机温度急剧上升,因而对供水可靠性的要求非常严格。一般有主、备水源,可互相切换,冷却水中断超过一定时限后要作用于事故停机。
2.自动化元器件配置
考虑机组推力与上导共槽、水导水润滑、发电机空冷情况下的需求,需配置以下元器件。
(1)信号元件(信号传感器)。冷却水总管监视器具(示流传感器)1只,如BAR系列抗震型靶式流量计,其公称口径为15~3000mm、公称压力为0.6MPa~42MPa,内置锂电池或外供24VDC、输出4~20mA、脉冲0~10V、RS-232/RS-485、GPRS无线远传,又如银亿通水流开关式传感器;水导润滑冷却水监视用示流传感器1只;监视上导推力、下导上限和下限油位用开关式传感器共4只;监式上导推力、下导温度过热(如55℃)和过高(如70℃)用开关式传感器共4只。共需PLC之输入开关量10点;另外,水轮发电机组的“机组开机继电器”、“机组运行状态标识”、“机组停机复归标识”等信号可由通信部分传送。
(2)执行元件(执行器)。总冷却水管控制用电磁配压阀1只,其ZT电磁铁吸引线圈、脱扣线圈分别控制阀的开启与关闭,线圈仅在动铁心动作时短时通电,吸引线圈与脱扣线圈分别用PLC的两个输出点控制;上导推力槽油位上限信号器1只;上导推力槽油位下限信号器1只;下导槽油位上限信号器1只;下导槽油位下限信号器1只;上导推力轴承温度过热(如55℃)指示器1只;上导推力轴承温度过高(如70℃)指示器1只;下导轴承温度过热(如55℃)指示器1只;下导轴承温度过高(如70℃)指示器1只;主、备润滑水投入与切除用的电磁配压阀各1只(3阀共6点);总冷却水管内冷却水中断报警输出1点;润滑水中断事故警输出1点;水轮机组润滑和冷却系统各事故停机信号汇总输出1点。共需PLC之输出开关量16点。
显然选用西门子S7-200 PLC是可以满足控制需求的。注意这里油位与温度信号的采集及输出控制没有使用模拟量,当然也可采集油位与温度的模拟量数值,然后与各设定数值进行比较,比较结果作为控制的动作条件。
3.PLC输入/输出点地址分配
SF-200 PLC分配输入/输出点地址分配见表4-3。
表4-3 S7-200 PLC输入/输出点地址分配
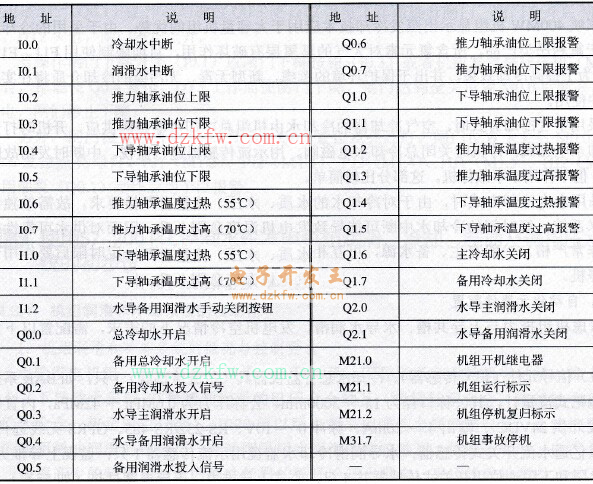
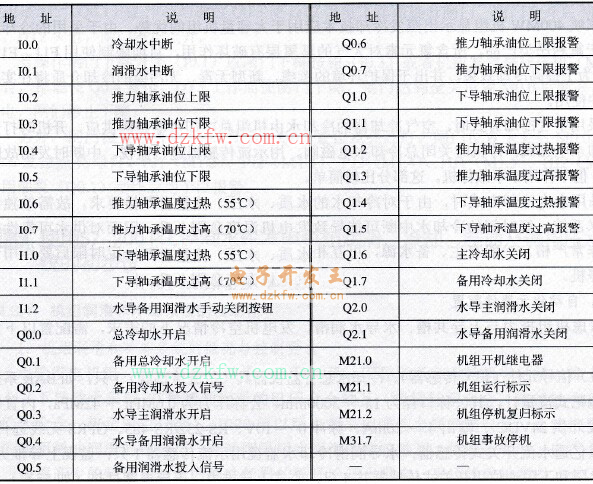
4.控制程序的初步拟定
通过分析水轮机组润滑和冷却系统的状况与控制要求,合理选择PLC控制系统硬件,运用好编程指令就可编制以下控制程序,如图4-6所示。
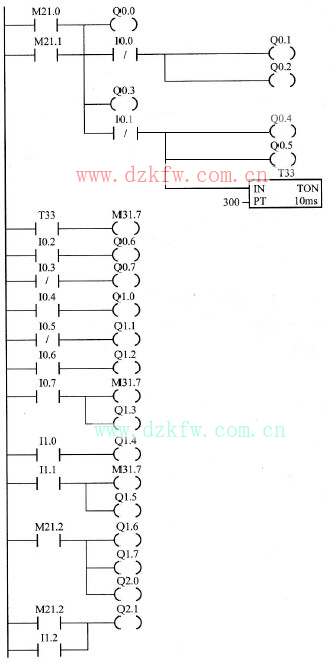
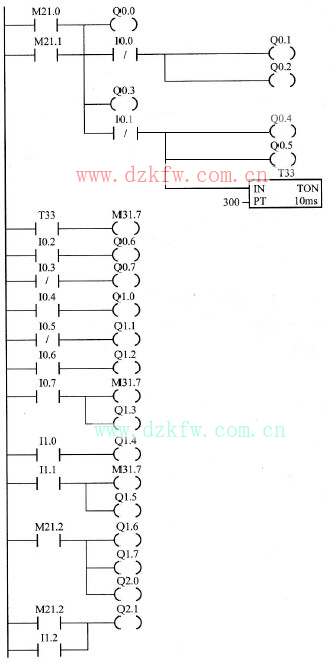
图4-6 润滑和冷却系统的S7-200 PLC控制程序
水轮机组润滑和冷却系统控制程序的语句表如下所示。
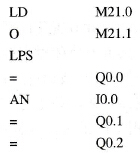
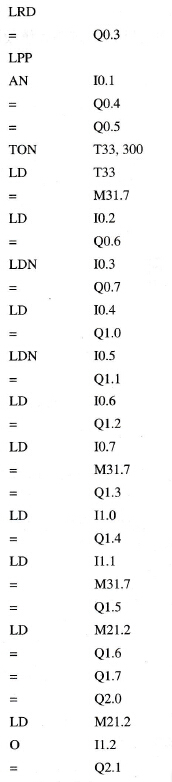
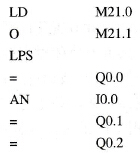
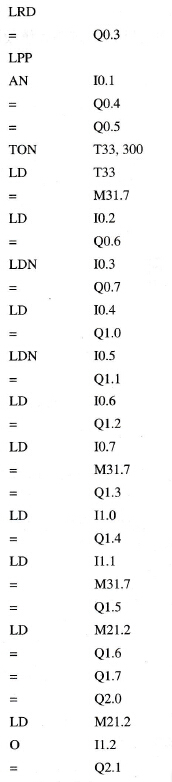
5.程序说明
开机继电器M21.0置位或者机组运行标示M21.1置位后,总冷却水由Q0.0置位而开起,水导主润滑水由Q0.3置位而开起。若开机或运行过程中冷却水中断,则I0.0常闭触点接通,备用总冷却水由Q0.1置位而投入,并由Q0.2置位而发出相应信号。若在开机或运行过程中润滑水中断,则I0.1常闭触点接通,水导备用润滑却水由Q0.4置位而投入,并由Q0.5置位而发出水导备用润滑水投入信号,同时水导备用润滑水中断时间用T33记录,其整定值为3s。若在整定时间(3s)到达时仍无润滑水,则作用于机组事故停机M31.7置位。
若达到推力轴承油位上限,则I0.2置位,再使Q0.6置位而报警。若达到推力轴承油位下限,则I0.3复位,再使Q0.7置位而报警。若达到下导轴承油位上限,则I0.4置位,再使Q1.0置位而报警。若达到下导轴承油位下限,则I0.5复位,再使Q1.1置位而报警。若推力轴承温度过热(55℃),则I0.6置位,再使Q1.2置位而报警。若推力轴承温度过高(70℃),则I0.7置位,一使M31.7置位而进行机组事故停机,二使Q1.3而发出推力轴承温度过高信号。若下导轴承温度过热(55℃),则I1.0置位,再使Q1.4置位而报警。若下导轴承温度过高(70℃),则I1.1置位,一使M31.7置位而进行机组事故停机,二使Q1.5而发出下导轴承温度过高信号。
当机组停机过程完成后,M21.2置位,一使Q1.6置位而关闭主冷却水,二使Q1.7置位而关闭可能打开了的备用冷却水,三使Q2.0置位关闭水导主润滑水,四使Q2.1置位关闭可能打开了的水导备用润滑水。另外,在水导主润滑水故障修复后,可以通过水导备用润滑水手动关闭按钮置位I1.2,从而使Q2.1置位关闭水导备用润滑水。
二、机组制动系统的自动化
机组与系统解列后,由于转子的巨大转动惯量储存着较大的机械能量,且风阻、液阻在转速变低后大幅度下降,故若不采取任何制动措施,则转子将较长时间处于低转速运行状态,这样对推力轴瓦润滑极为不利,有可能导致轴瓦在干摩擦或半干摩擦状态下运转,因此有必要采取制动措施以缩短停机时间。
通常的制动措施是:卸负荷并导叶全关后,当机组转速下降至35%nr(有液压减载装置的设置为10%nr)左右时,用压缩空气顶起设于发电机转子下面的制动闸瓦,即对转子进行机械制动,之所以不在停机时就加闸,是为了减少闸瓦的磨损。也可采用电气制动,停机时通过专设的开关将与系统解列的发电机接人制动用的三相短路电阻,为了提高低转速时的电气制动效果,可将发电机励磁绕组由变低了的励磁机电压改为厂用电整流供给。另外,冲击式水轮机一般采用水力制动,即设置专门的制动喷嘴,停机时打开它,将水流射到水斗的背面进行制动,这样可以在停机一开始就进行制动以缩短停机时间。
机组转动部分完全静止后,应撤除制动,以便下次启动。在停机过程中,如果导叶剪断销被剪断,个别导叶失去控制而处于全开位置,则为使机组不致于长时间低转速运转,应不撤除制动。
S7-200 PLC输入/输出点地址分配见表4-4,然后根据以上要求初步拟定的机组制动系统自动化程序如图4-7所示。
表4-4 S7-200 PLC输入/输出点地址分配
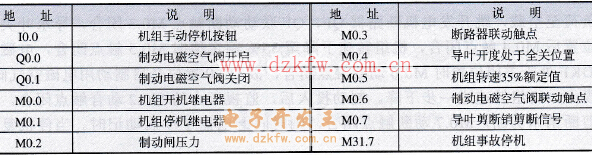
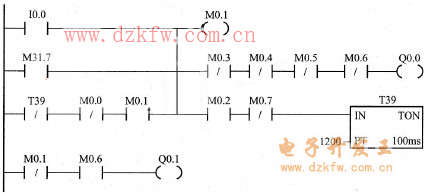
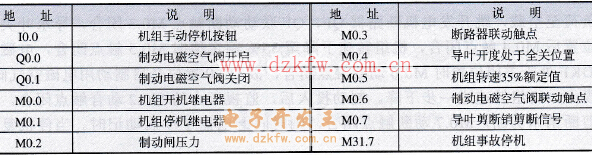
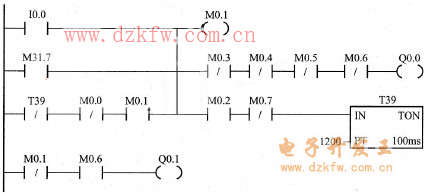
图4-7 机组制动系统自动化程序
机组制动系统控制程序的语句表如下所示。


程序说明:当操作机组手动停机按钮I0.0置位或机组事故停机M31.7置位时,机组停机继电器M0.1置位,如果此时没有要求再次启动机组,则开机继电器M0.0动断触点是闭合的,结合T39的动断触点,由M0.1动合触点闭合实现自保持。随后机组卸负荷至空载,跳开发电机断路器QF,QF联动动断触点M0.3闭合,导水叶关至全关位置后M0.4触点闭合,机组转速下降至35%额定值时M0.5触点闭合,电磁空气阀DKF处于关闭位置时M0.6动断触点闭合,故Q0.0置位开启制动用电磁空气阀,制动投入,机组转速进一步下降。制动投入后,监视压力的M0.2动合触点闭合,如此时剪断销未剪断,M0.7动断触点闭合,则时间继电器T39启动记时。当停机复归时间(一般为2min左右,由试验确定)到达后,T39动断触点打开,机组停机继电器M0.1自保持回路断开,M0.1复归并使Q0.1置位,关闭制动用电磁空气阀,撤除制动,停机过程即告结束。若剪断销已剪断,则T39不启动,M0.1自保持不解除,制动不撤除。
三、机组调相压水系统的自动化
电力系统缺乏无功功率时,可以利用水电站的闲置机组(如系统无事故时的备用机组、枯水期不能发电的机组、负荷低谷时的调峰与调频机组)作调相运行机组,此时机组从系统吸收少量有功功率,而输出较多的无功功率。水轮发电机组作调相运行时,导水叶是全关的,为了减少阻力和电能损耗,必须将水轮机转轮室水位压低,使转轮在空气中旋转。对机组调相压水系统自动化的要求如下所示。
(1)当机组转为调相运行时,打开主给气阀(可考虑与治理抬机用电动调节补气阀合二为一)将压缩空气送人转轮室将水位压下,下降至“封水效应”容许的下限水位时,关闭主给气阀。
(2)由于流道逸气、携气,转轮室水位逐渐上升至“风扇效应”容许的上限水位时,又自动开启主给气阀,将水位再次压低至下限水位。
(3)为避免主给气阀操作过于频繁,在主给气阀处并联一只由电磁配压阀控制的较小的辅助液压给气阀(进气流量略小于逸气流量+携气流量),它在调相过程中一直开启。
S7-200 PLC输入/输出点地址分配见表4-5,然后根据以上要求初步拟定的机组调相压水系统的自动控制程序如图4-8所示。
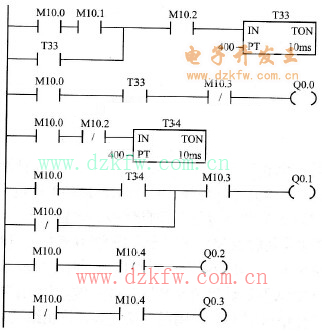
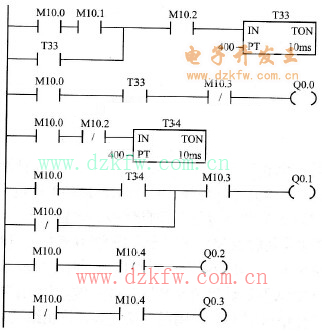
图4-8 机组调相压水系统的自动控制程序
表4-5 S7-200 PLC输入/输出点地址分配
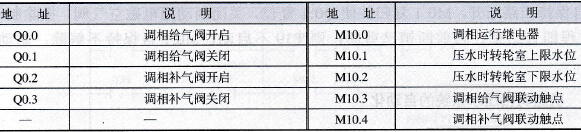
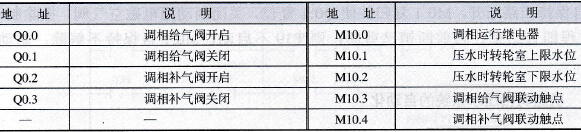
调相压水系统控制程序的语句表如下所示。
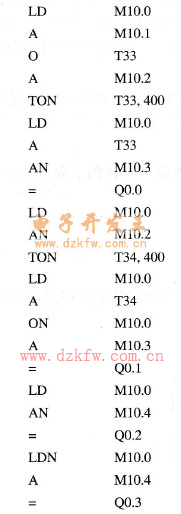
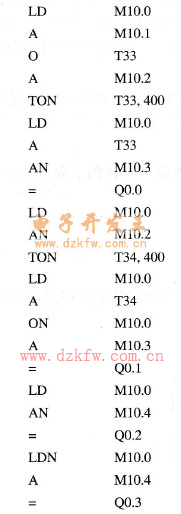
程序说明:当机组转入调相工况运行时M10.0置位,初始时转轮室充满着水(由于反汽蚀需要采用负吸出高),水位高于转轮室上限值时,M10.1置位并启动时间继电器T33,延时4s(确认不是瞬时情况)后T33置位(并自保持到转轮室下限水位M10.2动合触点断开),加上调相给气阀联动动断触点M10.3闭合,使Q0.0置位,开启调相给气阀,向转轮室送入压缩空气,将水位压下。当水位降至下限水位以下时,M10.2动断触点闭合以启动时间继电器T34,延时4s(确认不是瞬间情况)后T34置位,加上调相给气阀联动动合触点M10.3在阀开时已闭合,使Q0.1置位,关闭调相给气阀,停止给气。
同时,机组转入调相运行后,M10.0置位,加上调相补气阀联动动断触点M10.4闭合,使Q0.2置位而开启调相补气阀,只要机组处于调相工况运行,补气阀就一直打开。如果补气量不够,经过相当长的一段时间后,转轮室水位又上升至上限水位,M10.1置位、T33置位,使Q0.0置位又再次打开调相给气阀,将水位重新压下。
直到机组停止作调相运行,M10.0动断触点接通,Q0.3置位而关闭调相补气阀,此时Q0.1置位也关闭调相给气阀。
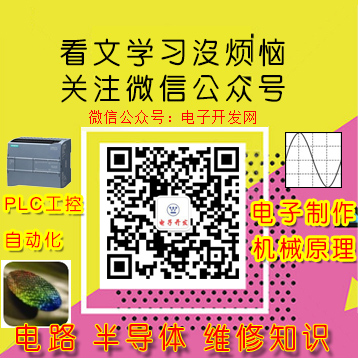