随着工业自动化的普及和发展,机械制造业对于机床的要求越来越高,随之出现了以减少劳动力、提高工作效率为目的的新型机床加工中心。加工中心是典型的集高新技术于一体的机械加工设备,是满足现代制造业的高科技机床,主要用于加工更换频繁及复杂、精度要求较高的零件,它的发展代表了一个国家设计和制造业的水平,已成为现代机床发展的主流方向。与普通数控机床相比,加工中心具有自动换刀装置,能自动更换刀具,在一次装卡中完成铣、镗、钻、扩、铰、攻丝等,工序高度集中,其加工效率和精度均高于普通机床。传统机床主要采用继电器一接触器进行控制,故障率高、可靠性差、维修工作量大,采用PLC控制系统可以很好地解决上述问题。本实例将讨论PLC在加工中心运动控制中的应用。
一、加工中心概述
加工中心的示意图如图8-11所示,图中左上侧为该加工中心使用的刀库,其中,T1、T2、T3为钻头,实现钻削功能;T4、T5、T6为铣刀,实现铣削功能。加工中心有三个坐标轴:X轴、Y轴、Z轴,分别由三个伺服电动机控制,实现加工中心的左右、前后和上下运动,同时,在X轴方向安装有检测工作台左右运动极限位置的两个限位开关,在Y轴方向安装有检测工作台前后运动极限位置的两个限位开关,在Z轴方向安装有检测工作台上下运动极限位置的两个限位开关。此外,该加工中心还有指示运动的运动指示灯以及指示三个轴向运动的指示灯,X灯、Y灯和Z灯,以及控制加工中心运动的运行控制按钮。
图8-11 加工中心示意图
二、控制系统硬件设计
1.系统输入/输出信号分析
PLC的输入信号共有10路,需占用10个输入端子,具体分配如下:控制加工中心运行的启动按钮,需1路输入信号;控制加工中心分别沿X轴、Y轴和Z轴运动的3个按钮,需3路输入信号;指示X轴方向左右运动极限的2个限位开关,指示Y轴前后运动极限的2个限位开关,指示Z轴方向上下运动极限的2个限位开关。
PLC的输出信号共有13路,需要13个输出端子,具体描述如下:指示加工中心正常运行的指示灯,接1个输出端子;控制三个钻头T1 - T3运动的3台电动机,需3个输出端子;控制3个铣刀运动的3台电动机,需3个输出端子;控制加工中心沿X轴、Y轴和Z轴运动的3台伺服电动机,需3个输出端子;以及控制X轴、Y轴和Z轴运动停止的3个输出信号,需3个输出端子。
2.PLC的输入/输出分配表
根据上述对加工中心输入/输出信号的分析,可编制如表8-2所示的PLC输入/输出分配表。
表8-2 PLC输入/输出分配表
序号 |
地址 |
名称 |
功能说明 |
10路数字输入信号 | |||
1 |
I0.0 |
按钮SB1 |
启动加工中心运动 |
2 |
I0.1 |
按钮SB2 |
控制X轴运动 |
3 |
I0.2 |
按钮SB3 |
控制Y轴运动 |
4 |
I0.3 |
按钮SB4 |
控制Z轴运动 |
5 |
I0.4 |
限位开关 |
X轴方向左到位 |
6 |
I0.5 |
限位开关 |
X轴方向右到位 |
7 |
I0.6 |
限位开关 |
Y轴方向前到位 |
8 |
I0.7 |
限位开关 |
Y轴方向后到位 |
9 |
I1.0 |
限位开关 |
Z轴方向上到位 |
10 |
I1.1 |
限位开关 |
Z轴方向下到位 |
13路数字输出信号 | |||
1 |
Q0.0 |
接指示灯 |
运行指示 |
2 |
Q0.1 |
钻头电动机 |
T1钻头 |
3 |
Q0.2 |
钻头电动机 |
T2钻头 |
4 |
Q0.3 |
钻头电动机 |
T3钻头 |
5 |
Q0.4 |
铣刀电动机 |
T4为铣刀 |
6 |
Q0.5 |
铣刀电动机 |
T5为铣刀 |
7 |
Q0.6 |
铣刀电动机 |
T6为铣刀 |
8 |
Q0.7 |
控制伺服电动机 |
X轴,1为左移,0为右移 |
9 |
Q1.0 |
控锅伺服电动机 |
Y轴,1为前移,0为后移 |
10 |
Q1.1 |
控制伺服电动机 |
Z轴,1为上移,0为下移 |
11 |
Q1.2 |
控制伺服电动机 |
停止X轴运动 |
12 |
Q1.3 |
控制伺服电动机 |
停止Y轴运动 |
13 |
Q1.4 |
控制伺服电动机 |
停止Z轴运动 |
3.PLC选型
根据表8-2中的输入/输出分配情况,参看第2章中的表2-1,本控制实例中的PLC可选用西门子公司S7 - 200系列中的小型PLC - CPU226。
4.PLC硬件接线图
根据前述介绍,可设计如图8 -12所示的PLC硬件接线图。
图8-12 PLC硬件接线图
三、控制系统程序设计
(1)加工流程。为了向读者介绍加工中心的PLC控制实例,本节用一个典型的加工流程来阐述PLC在加工中心控制中的具体情况,该加工过程的流程图如图8 13所示。该加工流程包含6组运动,可划分为18个步骤,本实例中用位存储器M11.0~M11.7、M12.0~M12.7、M13.0~M13.1的状态来控制这18个步骤。首先产生周期为3s的脉冲,按下启动按钮,延时3s,使M10.0为1,然后以脉冲的速度右移,使位存储器M11.0~M11.7、M12.0~M12.7、M13.0~M13.1分别为1。
图8-13 加工中心自动控制流程图
动作过程描述如下:启动加工中心,运动指示灯Q0.0亮,选用T1钻头,首先启动X轴方向伺服电动机(Q0.7),使加工中心从零位开始沿X轴运动(M11.0为1),运动到指定的位置后,X轴方向停止运动,Z轴(Q1.1)向下运动,达到指定位置后,T1钻头(Q0.1)开始钻孔(M11.1为1)。该工步完成后,Z轴向上运动到指定位置,退下T1钻头(M12.1为1),换上T2钻头。然后加工中心沿Y轴(Q1.0)运动(M11.3为1),达到指定位置后停止,再沿Z轴向下运动,达到指定位置后停止,开始T2钻头(Q0.2)钻孔(M11.4为1)。T2钻头钻完孔后,Z轴向上运动到指定位置后退下T2钻头(M11.5为1),换T3钻头。然后控制加工中心分别沿X轴(Q0.7)和Y轴(Q1.0)运动到指定位置(M11.6为1),然后控制加工中心沿Z轴(Q1.1)向下运动到指定位置,控制T3钻头(Q0.3)钻孔(M11.7为1)。该工步完成后,控制加工中心沿Z轴(Q1.1)向上运动到指定位置后停止,退钻头T3(M12.0为1)、换铣刀T4 (Q0.4)。然后控制加工中心沿Z轴(Q1.1)向下运动到指定位置,T4铣刀运动(M12.1为1),沿X轴( Q0.7)执行铣削加工(M12.2为1)。该工步完成后,控制加工中心沿Z轴(Q1.1)向上运动到指定位置后退刀(M12.3为1),换铣刀T5。然后控制加工中心沿Z轴(Q1.1)向下运动到指定位置,T5铣刀(Q0.5)运动(M12.4为1),沿Y轴进行铣削加工(M12.5为1)。该工步完成后,控制加工中心沿Z轴(Q1.1)向上运动到指定位置后退刀(M12.6为1),换铣刀T6。然后控制加工中心沿Z轴(Q1.1)向下运动到指定位置,T6铣刀(Q0.6)运动(M12.7为1),控制T6铣刀沿和X轴(Q0.7)、Y轴(Q1.0)执行铣削加工(M13.0为1)。该工步完成后,控制加工中心沿Z轴(Q1.1)向上运动到指定位置后退刀(M13.1为1),至此该加工流程结束。
其中:运动指示灯(Q0.0)点亮的条件是I0.0为1;T1钻头(Q0.1)运动的条件是M11.1为1;T2钻头(Q0.2)运动的条件是M11.4为1;T3钻头(Q0.3)运动的条件是M11.7为1;T4铣刀(Q0.4)运动的条件是M12.1为1;T5铣刀(Q0.5)运动的条件是M12.4为1;T6铣刀(Q0.6)运动的条件是M12.7为1;加工中心沿X轴方向(Q0.7)运动的条件是M11.0、M11.6、M12.2和M13.0为1;沿Y轴方向(Q1.0)运动的条件是M11.3、M11.6、M12.5和M13.0为1;沿Z轴方向(Q1.1)运动的条件是M11.0、M12.2、M11.4、M11.5、M11.7、M12.0、M12.1、M12.3、M12.4、M12.6、M12.7和M13.1为1。
为了更好地阐述PLC在数控加工中心控制系统中的应用,本实例采用自动编程和手动编程两种方法,来对加工中心进行控制,首先介绍自动编程方法。
(2)自动控制编程。
自动控制梯形图程序如图8-14所示。
图8-14 自动控制梯形图
(3)手动编程。为使读者更好地理解加工中心的PLC编程原理,本部分针对下述动作流程编写手动控制程序,动作过程描述如下:
1)按下“运行控制”开关,启动系统,运行指示灯亮(Q0.0为1)。加工中心沿X轴方向向左运动(Q0.7为1),带动工件沿X轴向左运动。
2)到达“X左”限位,此时工件到达指定位置。然后T钻头沿Z轴向下运动,对工件进行钻孔。
3)到达“Z下”限位,T1钻头对工件进行钻孔加工。
4)钻孔完毕,T1钻头沿Z轴向上运动,返回刀库,达到“Z上”限位,系统将自动取铣刀T5,准备对工件进行铣削加工,铣刀T5沿Z轴向下运动。
5)到达“Z下”限位,Z轴停止运动,使加工中心沿Y轴方向向前运动(Q1.0为1),对工件进行铣削加工。
6)达到“Y前”限位,铣刀对工件加工完毕,然后使加工中心沿Z轴向上运动(Q1.1复位为1),系统进入退刀状态。
7)到达“Z上”限位,铣刀T5回刀库,复位,进入下一轮加工循环。
该动作流程所对应的梯形图8-15所示。
图8-15 手动控制梯形图
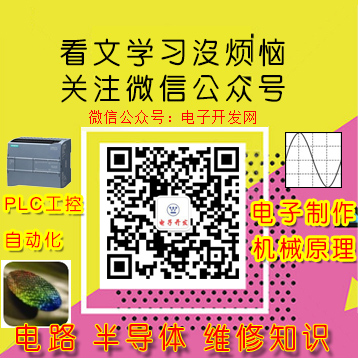