一、 日常常见使用场景
1、动作延时实现工艺要求
这恐怕是定时器出现的最先原因,比如工作台工进到位后在保持一定时间才退刀,以保证加工质量。又如在压装机,压力达到后维持一定时间,使压装效果良好。
2、动作延时使信号采集可靠
这种用法在工件测量中很常见。比如液压工作台将工件举起,检测机构根据工件的厚度判断其是否加工过。(又如测头前进,根据零件尺寸判断工件类型,都类同)。
这时就需要使用一个定时器,使液压工作台动作到位一定时间后再采集检测机构的信号,才能准确可靠。
3、信号延时确保安全
在传送带动作及有干涉危险的动作中,为确保安全,往往将到位信号延时作为下一步动作的条件之一。
4、机械液压动作故障监测
动作在规定时间内未到位则报警,这样既有很好的自诊断功能,又能保障部件的安全。如机械滑台可能因阻死而无法到位,可以及时断开电机电源避免长时间过载运行。
一般用一个定时器实现正反向动作监测(当然如果正反向动作时间相差太大,如工进速度较慢的滑台,则需使用两个):
5、 液压压力、流量传感器的监控
这类传感器和上述动作到位传感器有点区别,就是动作激活一定时间后接通,动作断开一定时间后才断开。
6、 间歇性动作
如定时润滑,定时走纸等场合。
二、 特殊使用场景
有些场合巧妙地使用定时器或替代设计,可以达到巧妙的效果。
1、脉冲吹气(断续输出)
在清洗机中经常遇到脉冲吹气的场合:隔m秒吹n秒。
这种情况最易想到的是使用两个定时器,一个m秒,一个n秒,先后触发,即m秒定时完激活n秒定时器,与此同时激活吹气输出,待n秒定时完再切断输出,同时激活下一轮的m秒定时,如此周而复始直到脉冲吹气结束。
然而这样的设计有些烦琐,而且还稍有点难度。我们注意到,许多PLC系统中,定时器都有相应的定时完成(timer-done)状态位及定时当前值(timer-value)状态字。巧妙地运用这两个状态变量,我们使用一个m+n秒定时器,就可以简单明了地编写出这个程序来。
此外,指示灯闪烁也可以用这种方法编程。现在的PLC系统大都有系统固有的位变量,直接具有闪烁功能,只是它亮和灭的时间是相等的,这种情况其实是上述编程的一种特例而已。(即m=n的情况)
2、 链条传动监测(断续输入监测)
链条传动监测一般采用接近开关,如图A处(感应块在轴上),或B处(感应块在链条上)。这样的情况属于断续输入,即链条运转时,接近开关输入既不能始终为0,也不能始终为1。
如果使用定时器编程,我们同样需要两个定时器如下:
注意接近开关在任何情况下只能取0和1两种状态之一,所以这里的timer-value1和timer-value2不能合二为一。
以上编程并不复杂,但为此使用两个定时器总觉得有点“奢侈”,特别是在功能块数目不多的小型PLC,如果要监测的东西多了,定时器就会不够用。
于是有些程序设计者“发明”了另外一种定时器:运用字变量word,每个扫描循环加1,所以word变量的值就代表经过的扫描次数,它乘上扫描周期就可以大致地表征定时时间了。
由于每个扫描周期不尽相等,(它因程序执行而每个周期都在波动,略有差别),所以这样的定时器方法并不精确,在前面所述的实现工艺要求延时等场合不宜使用,但在其它许多场合则很实用。例如这个链条监控的程序,用一个WORD变量就够了。而字变量相对多得多,可以说大大扩充了定时器的数量。
3、 电机启动过程中的定时
在电机启动过程中有许多场合要用到定时器,机床设计中有时用硬件定时,有时用软件定时。
(1)、分时启动,错开高峰
由于电机启动冷电流大,所以在有多台电机时经常采用分时启动方案。
(2)、定时切除启动电阻
在大功率电机降压启动过程中,需要逐级切除电阻,在不装备电压电流或转速检测装置的情况下,可以采用定时的方法切除电阻。
(3)、定时脉冲启动法
在一种三菱磨床上见到一种特殊的启动方式,它既无变频器,又无软启动,也没有启动电抗,启动时,接触器吸合2S,在断开2S,此时砂轮已开始缓慢运转;然后再吸合2S,再断开2S,如此反复三次,使砂轮由慢到快完成启动过程。这种方法每次吸合时都有较大冲击,但效果比一次吸合启动要好。这种方法可以借鉴,笔者给它取名为“脉冲启动法”。
4、 延时抽取
地泵电机在液面上限传感器发讯后启动,如果没有装备液面下限传感器,一般采用延时运转一定时间后停泵的方法。
此外单向限温的加热或冷却装置也采用类似的办法。当然,这类情况使用单稳态也很好。
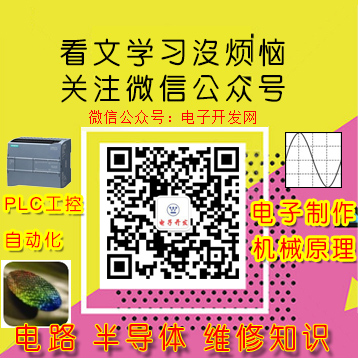