随着电子技术特别是电子计算机的广泛应用,机器人的研制已经成为高技术领域内迅速发展起来的一门新兴技术,它更加促进了机械手的发展,使得机械手能更好地实现与机械化和自动化的有机结合。机械手不仅对环境适应性强、能持久、耐劳、动作准确、灵活性好、能很好地适应产品的不断变化,而且提高了工作效率,节省了大量的劳动力,因此机械手已经受到很多部门的重视,在工业生产中得到了愈来愈广泛的应用。本节将对机械手的PLC控制过程进行详细说明。
一、工艺流程与操作方式
图8-1所示为搬运机械手的工作示意图,该机械手是一个水平/垂直位移的机械设备,运动过程并不复杂,一共有6个动作,分为3组,即上升/下降、左移/右移、夹紧/放松。其操作是将工件从左工作台搬到右工作台,由重新接近开关来检测工作台上有没有工件。
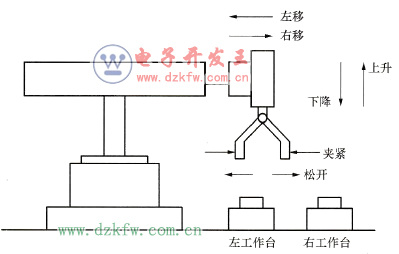
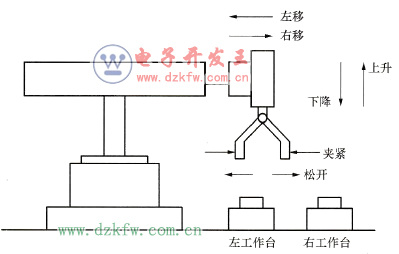
图8-1 搬运机械手工作时的动作
机械手通常位于原点,所有的动作均由气缸驱动,而气缸则由相应的电磁阀控制。其中,上升与下降、左移与右移动作均由双线圈二位电磁阀控制,即当下降电磁阀通电时,机械手下降;下降电磁阀断电时,机械手停止下降。只有当上升电磁阀通电时,机械手才上升。机械手的夹紧和放松由一个单线圈二位电磁阀(称为夹紧电磁阀)来控制,线圈通电时夹紧,断电时放松。
(1)机械手工艺流程。机械手的动作顺序和检测元件、执行元件的布置示意图如图8-2所示。机械手的初始位置停在原点,按下启动按钮后,下降电磁阀通电,机械手下降,下降过程中,碰到下限位开关时,下降电磁阀断电,下降动作停止。同时接通夹紧电磁阀,机械手夹紧工件,夹紧后,上升电磁阀通电,机械手上升。上升过程中,碰到上限位开关时,上升电磁阀断电,上升过程停止。同时接通右移电磁阀,机械手右移。右移过程中,碰到右限位开关时,右移电磁阀断电,右移过程结束。如果此时工作台上没有工件,则光电开关接通,下降电磁阀通电,机械手下降。下降过程中,碰到下限位开关时,下降电磁阀断电,下降过程结束。同时夹紧电磁阀断电,机械手放松,在合适的位置放下工件。放完工件后,上升电磁阀通电,机械手上升,上升过程中,碰到上限位开关时,上升电磁阀断电,上升过程结束。同时接通左移电磁阀,机械手向左移动,直到碰到左限位开关后,左移电磁阀断电,左移过程结束,此时机械手回到原点。至此,机械手完成了一个周期的动作。
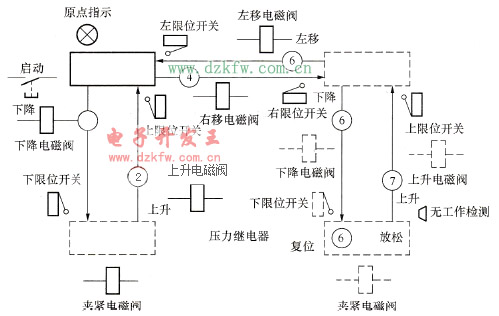
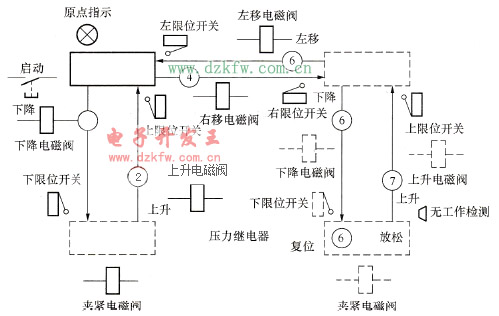
图8-2 搬运机械手的动作顺序和检测元件、执行元件的布嚣示意图
为保证安全,当机械手右移到位准备下降时,必须确保右工作台上没有工件时才能下降,若上一次搬到右工作台上的工件尚未移走,机械手应自动暂时等待。可以使用一个光电开关来检测右工作台上有无工件。
(2)操作方式。搬运机械手的操作方式可化分为手动操作和自动操作两类,自动操作又可进一步划分为单步、单周期以及连续操作。
1)手动操作。利用按钮对机械手的每一个动作单独进行控制,例如,选择夹紧/放松运动时,按下启动按钮,机械手夹紧;按下停止按钮,机械手放松。上下运动时,按下“下降”按钮,机械手下降,按“上升”按钮,机械手上升。
2)单步操作。每按一下启动按钮,机械手完成一步的动作后自动停止。
3)单周期操作。按下启动按钮,从原点开始,机械手自动完成一个周期的动作,返回原点后停止。
4)连续操作。机械手从原点开始,每按一次启动按钮,机械手将按工序自动反复连续循环工作,直到按下停止按钮,机械手自动停机。
二、硬件设计
(1)操作面板设计。根据以上控制要求以及操作方式,可设计如图8-3所示的操作台面板布置示意图。
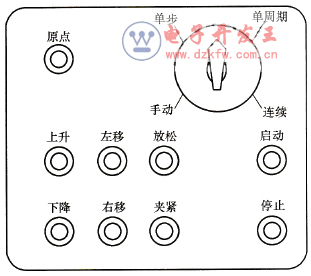
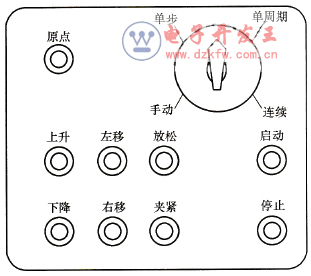
图8-3 操作台面板布置示意图
(2)输入、输出信号分析。输入信号是将机械手的工作状态和操作信息提供给PLC,PLC的输入信号共有18个输入信号点,需占用18个输入端子。具体分配如下:“操作方式”选择开关有手动、单步、单周期和连续4种工作方式,需要4个输入端子;手动操作时,需要下降、上升、右移、左移、夹紧、放松、回原点7个按钮,需要7个输入端子;自动工作时,需要启动按钮、停止按钮,需要用2个输入端子;位置检测信号有上限、下限、左限、右限4个行程开关,需要4个输入端子;“无工件”检测信号采用光电开关作检测元件,需要1个输入端子。总计需要18个输入端子。
输出信号用来控制机械手的上升、下降、左移、右移和夹紧5个电磁阀线圈,需要5个输出点;此外,机械手从原点开始工作,需要1个原点指示灯,要占用1个输出端子。所以,共需要6个输出端子。
(3) PLC的输入/输出分配表。根据对机械手的输入/输出信号的分析,可编写如表8-1所示的PLC输入/输出分配表。
表8-1 PLC输入/输出分配表
序号 |
地址 |
名称 |
功能说明 |
18路数字输入信号 | |||
1 |
I0.0 |
按钮 |
启动机械手动作 |
2 |
I0.1 |
限位开关 |
指示机械手的运动下限 |
3 |
I0.2 |
限位开关 |
指示机械手的运动上限 |
4 |
I0.3 |
限位开关 |
指示机械手的右移运动极限 |
5 |
I0.4 |
限位开关 |
指示机械手的左移运动极限 |
6 |
I0.5 |
光电开关 |
检测工作台上有无工件 |
7 |
I0.6 |
按钮 |
停止机械手工作 |
8 |
I0.7 |
选择开关 |
手动操作方式选择开关 |
9 |
I1.0 |
选择开关 |
单步操作方式选择开关 |
10 |
I1.1 |
选择开关 |
单周期操作方式选择开关 |
11 |
I1.2 |
选择开关 |
连续操作方式选择开关 |
12 |
I1.3 |
按钮 |
选择下降运动 |
13 |
I1.4 |
按钮 |
选择上升运动 |
14 |
I1.5 |
按钮 |
选择右移 |
15 |
I1.6 |
按钮 |
选择左移 |
16 |
I1.7 |
按钮 |
选择夹紧动作 |
17 |
I1.8 |
按钮 |
选择放松动作 |
18 |
I1.9 |
按钮 |
复位按钮,使机械手复位 |
6路数字输出信号 | |||
1 |
Q0.0 |
电磁阀 |
控制机械手的下降移动 |
2 |
Q0.0 |
电磁阀 |
控制机械手的夹紧动作 |
3 |
Q0.2 |
电磁阀 |
控制机械手的上升移动 |
4 |
Q0.3 |
电磁阀 |
控制机械手向右移动 |
5 |
Q0.4 |
电磁阀 |
控制机械手向左移动 |
6 |
Q0.5 |
指示灯 |
指示机械手是否回到原点 |
(4) PLC选型。根据表8-1所示的输入/输出分配表,参看第2章中的表2-1,本实例中PLC选用西门子公司生产的S7-200系列PLC中的CPU226,S7-200 CPU226共有24个输入端子,16个输出端子,采用继电器输出型,完全可以满足本实例的控制需求。
(5) PLC硬件接线图。根据前述的输入/输出信号分析,可设计如图8-4所示的PLC的输入/输出接线图。
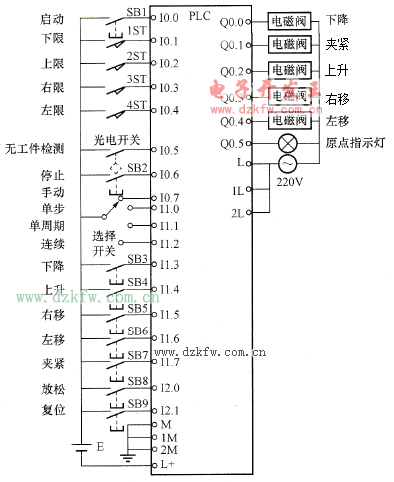
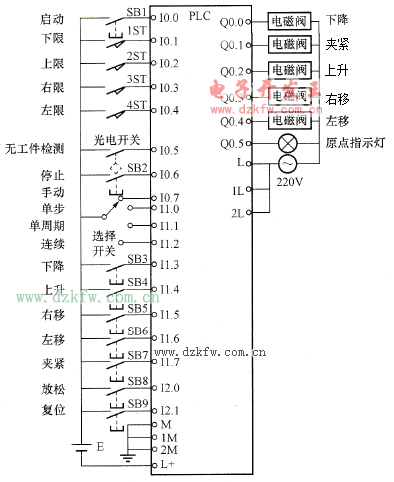
图8-4 PLC控制的机械手的外部接线图
三、PLC控制系统程序设计
为了便于编程,在设计软件时常将公用程序、手动程序和自动程序分别编出相对独立的程序段,再用条件跳转指令进行选择。搬运机械手的控制系统程序结构框图如图8-5所示。系统运行时首先执行公用程序,然后当选择手动工作方式时,I0.7接通并跳转至手动程序执行;当选择自动工作方式,然后当选择手动工作方式时,I0.7接通并跳转至手动程序执行;当选择自动工作方式(单步、单周期、连续)时,I1.0、I1.1或I1.2接通则跳转至自动程序执行。
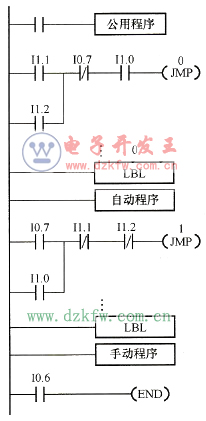
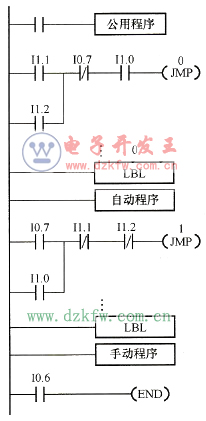
图8-5 控制系统程序结构框图
(1)公用程序。公用程序用于处理各种工作方式都要执行的任务,以及不同的工作方式之间相互切换的处理,公用程序如图8-6所示。


图8-6 公用程序
左限位开关I0.4、上限位开关I0.2的动合触点和表示机械手夹紧的Q0.1的动断触点的串联电路接通时,“原点条件”S0.0变为ON。当机械手处于原点状态(S0.0为ON),在开始执行用户程序(SM0.1为ON)、系统处于手动状态或自动回原点状态(I0.7或I2.1为ON)时,初始步对应的M0.0将被置位,为进入单步、单周期和连续工作方式做好准备。如果此时S0.0为OFF状态,M0.0将被复位,初始步为不活动步,按下启动按钮也不能进入步M2.0,系统不能在单步、单周期和连续工作方式下工作。
(2)手动程序。手动操作不需要按工序顺序动作,所以可按普通继电器程序来设计。手动操作的梯形图如图8-7所示。手动按钮I0.7、I1.3~I2.1分别控制下降、上升、右移、左移、夹紧、放松和回原点各个动作。为了保证系统的安全运行设置了一些必要的连锁。其中在左移动、右移动的梯形图中加入了I0.2作为上限连锁,因为机械手只有处于上限位置时,才允许左右移动。
(3)自动操作流程图。由于自动操作的动作较复杂,可先画出自动操作流程图,如图8-8所示,用于表明动作的顺序和转换条件,然后再根据所采用的控制方法设计程序。矩形框表示“工步”,相邻两工步用有向线段连接,表明转换的方向。小横线表示转换的条件,如转换条件得到满足,则程序从上一工步转到下一工步,步进控制原理如图8-9所示。
(4)自动程序设计。根据自动操作流程就可以画出自动控制程序的梯形图,如图8-10所示。
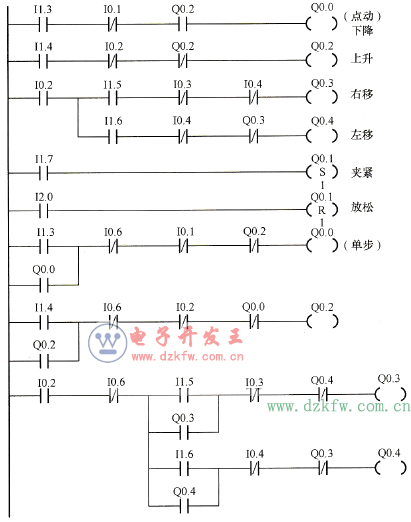
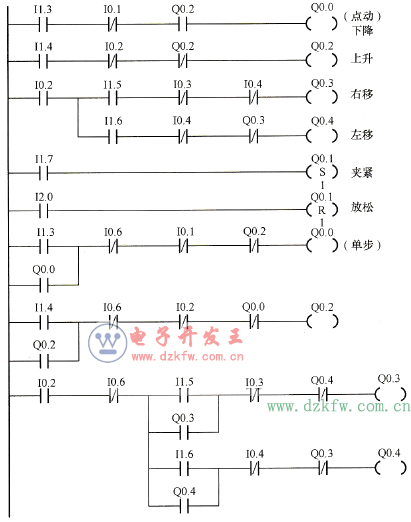
图8-7 手动操作的梯形图
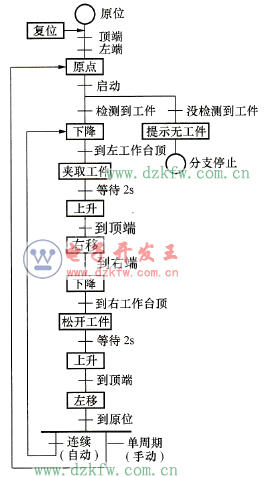
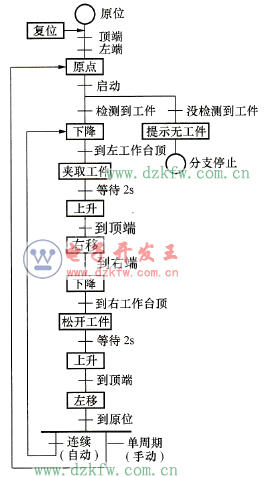
图8-8 自动操作流程图
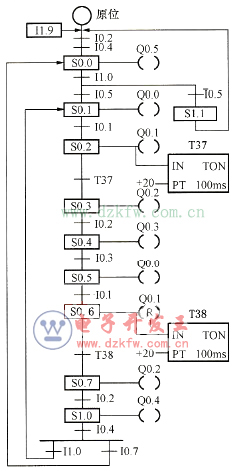
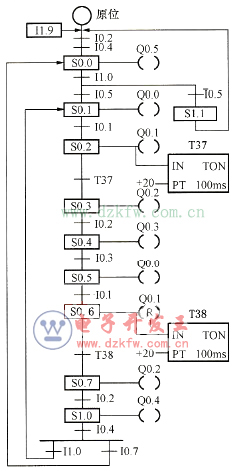
图8-9 步进控制原理图
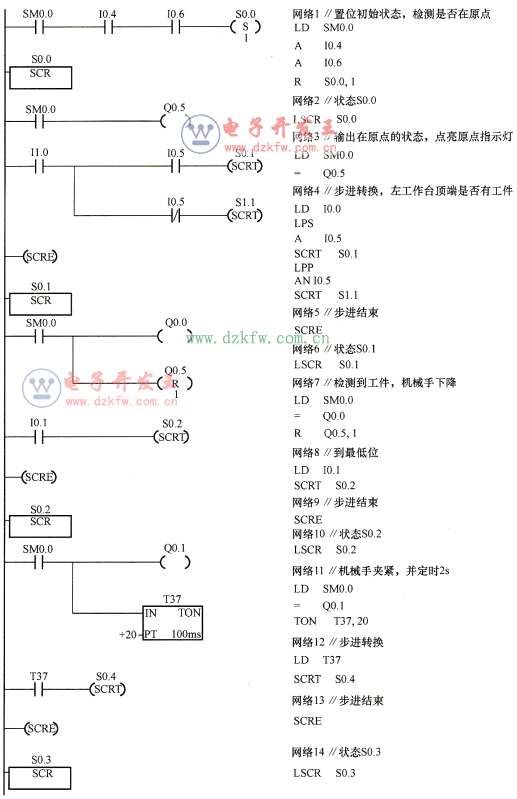
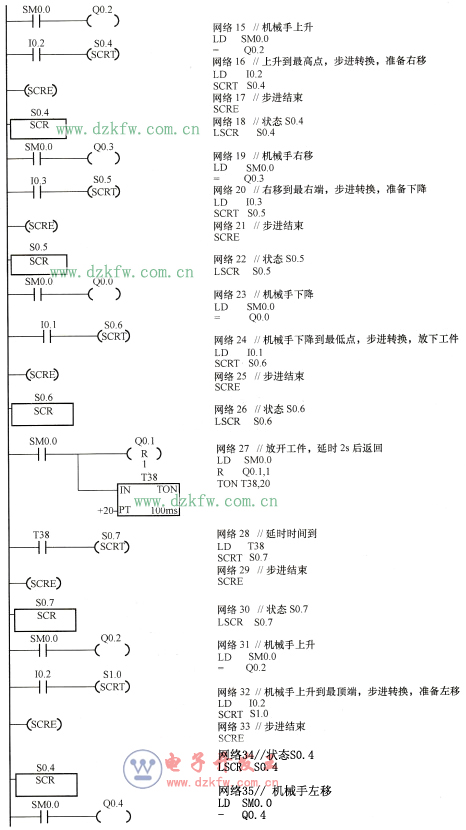
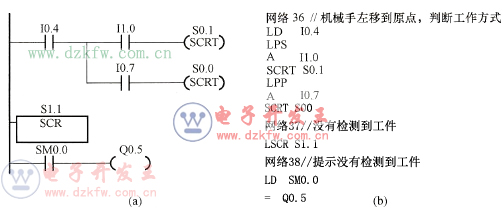
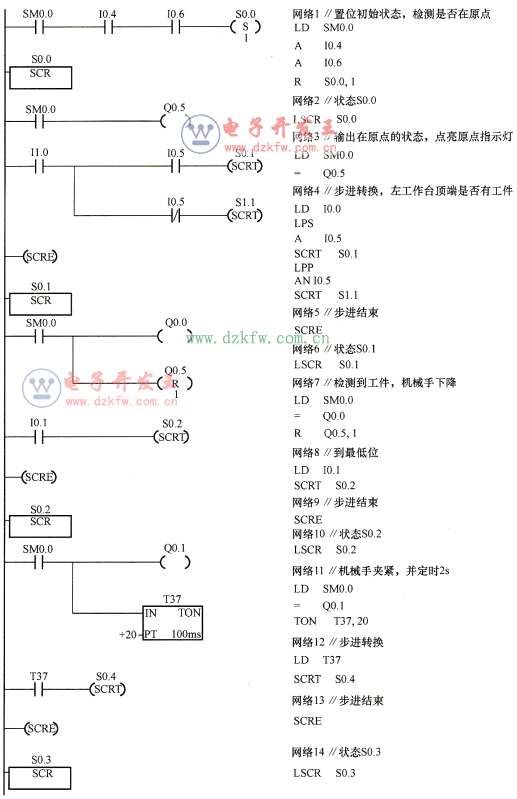
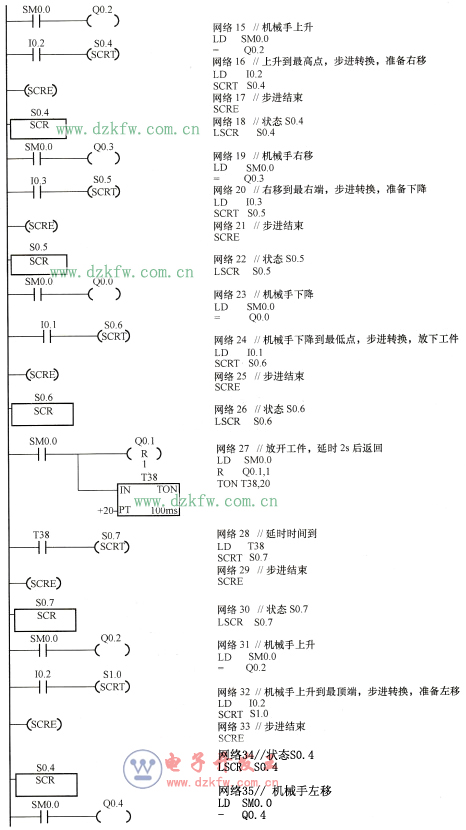
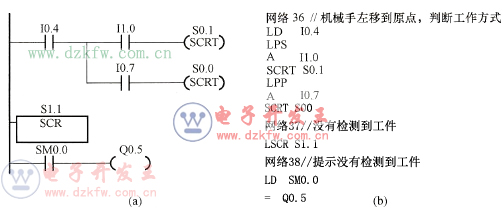
图8-10 自动控制方式梯形图
(a)梯形图;(b)语句表
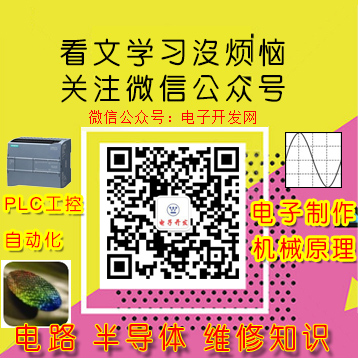