内齿轮副
由一个外齿轮和一个内齿轮组成的共轭齿轮副(图6-44)。多用于行星轮系中。常用内齿轮副有:平行轴内齿轮副(包括直齿、斜齿、人字齿);相交轴内齿轮副;交错轴内齿轮副(用的较少)。内齿轮副和外齿轮副相比,有下列特点:结构紧凑、诱导曲率半径大、重合度大、瞬时啮合齿数多,工作平稳、噪声小;滑动系数小;承载能力大;目前内齿轮加工稍有困难,设计要求严格,否则可能发生各种干涉现象。
平行轴内啮合渐开线直齿圆柱齿轮副
由一个渐开线圆柱外齿轮和一个相配的渐开线圆柱内齿轮组成的平行轴齿轮副。其啮合特性除具有平行轴渐开线圆柱齿轮副的全部啮合特性外,还具有:共轭齿面呈凸凹啮合,诱导曲率半径大,接触强度高;滑动系数小,润滑条件优,抗胶合能力强,耐磨损;啮合齿数多,重合度大,噪声小,工作平稳;结构紧凑等特点,但设计较复杂,当参数选择不当时,可能引起啮合干涉或切齿干涉、安装干涉。
平行轴内啮合渐开线斜齿圆柱齿轮副
由相配的渐开线斜齿外齿轮与渐开线斜齿内齿轮组成的平行轴内啮合圆柱齿轮副。见“平行轴渐开线圆柱齿轮副”与“斜齿内齿轮副”。
内啮合人宇齿圆柱齿轮副
由相配的一个人字齿圆柱外齿轮与一个人宇齿圆柱内齿轮组成的齿轮副,一般是指“平行轴内啮合渐开线人字齿圆柱齿轮副”。它具有斜齿内齿轮副的所有啮合特性,又具有在工作过程中能自行平衡轴向力的性能。由于人字齿轮可采用较大的螺旋角,所以斜齿轮副的啮合特性更为明显。
渐开线少齿差内齿轮副
齿数差很少(z2-z1=l~4)的一对相啮渐开线齿轮组成的内齿轮副。多用于渐开线少齿差行星齿轮传动,而单独作为传动机构的少齿差内齿轮副则很少,因为它不但不能获得较大传动比,而且在设计、制造、安装等方面很麻烦。
渐开线少齿差内齿轮副用于渐开线少齿差行星齿轮传动时,齿数差Δz=z2-z1越小,传动比越大,对于 ha*=1、a=20°的渐开线内齿轮副Δz小到某一数值,将产生各种干涉现象。为了避免干涉,使内齿轮副正常工作,在设计少齿差内齿轮副时通常采用三种方法:其一,采用短齿,即使ha*<1 ,常用的齿形参数是ha*=0.75~0.8,a=20°,c*=0.3~0.45;其二,合理地采用变位方法和变位系数;其三,增大刀具的齿形角,由于刀具是标准参数,改变齿形角较为困难,很少应用。三种方法中第二种方法比较有效、合理,故最为常用。其具体变位方法的选择和设计计算可参考有关资料。内齿轮副的各种干涉现象和避免方法可参考有关条目。
啮合角为零时的内齿轮副
零齿差的内齿轮副,rb1=rb2,两基圆重合节点落在基圆上,rb1=r1′,rb2=r2′,这时啮合线和基圆公切绥的夹角为零,即啮合角a′=0。另外若设计的内齿轮副rb1=r1′,rb2=r2′,这时两基圆在P点内切,所以过节点P作的啮合角亦为零。由图6-45可知,当啮合角为零时,必然产生内齿轮副的齿廓重迭干涉。若用插齿刀加工也将产生顶切。为了避免a′=0时的齿廓重迭干涉,应采用负变位的外齿轮和正变位的内齿轮,或采用切向变位。
平行轴内啮合渐开线圆柱齿轮副端面有效共轭齿廓
平行轴内啮合渐开线圆柱齿轮副,端平面内共轭点在齿面上的集合线,称端面有效共轭齿廓。有效共轭齿廓可用作图法求得。如图6-46所示:顶圆ra1交N1N2于B1,以o2B1为半径作圆交大齿轮齿廓于a′,则 为有效齿廓。同样,顶圆ra2交N1N2于B2,以 o1B2为半径作圆,交小齿轮齿廓于b′,则
为小齿轮的有效齿廓。
负啮合角
用插齿刀加工内齿轮时,若插齿刀的齿数过多,可能产生负啮合角现象,这时插齿刀和内齿轮的两个基圆不相交,啮合线无法作出,不可能实现正确啮合,也无法加工出正确齿形。故要避免负啮合角产生,根据无侧隙啮合方程式,可得出不产生负啮合角的条件。
渐开线内齿轮的径向变位
目前,渐开线内齿轮多用插齿刀切制(图6-47a),若在切齿时,相对改变刀具与齿轮坯的位置(图6-47b),亦可切削出径向变位的渐开线内齿轮。插齿刀实际上是一个变位齿轮,在不同端面内(前刃面内),具有不同的变位系数,x0=0的前刃面称原始截面,约定:用原始截面插齿刀加工齿轮,当刀具由加工标准齿轮时的位置远离被加工齿轮的中心,使机床中心距增大者,变位系数取正值,反之取负值,加工出来的内齿轮分别为正变位齿轮和负变位齿轮。加工内齿轮与加工外齿轮相比,由于变位引起的齿轮几何尺寸变化之间的主要区别在于齿厚与公法线的不同,正变位内齿轮不是增大而是减小。
为便于计算,把内齿轮的齿槽看成外齿轮的轮齿,这个假想的外齿轮用齿条刀具加工时的变位系数,作为内齿轮的变位系数图6-47c,这时就可以用相应的外齿轮的计算公式、图表等。但内齿轮的齿根高、齿根圆直径是用插齿刀加工时机床中心距a0确定的。
内齿轮副的负啮合现象内齿轮副或插齿刀与齿轮坯的啮合,若其啮合角a′(或a0′)<0称负啮合现象,这种现象产生的结果是,两齿轮(或刀具与齿坯)的基圆不相交,没有公切线,这对渐开线齿轮形不成啮合线,无法正常工作。所以负啮合现象不允许产生,于是必须满足条件a′(或a0′)>0,这时:
渐开线内齿轮副几何尺寸图标注着渐开线内齿轮副各个尺寸和名称(可用代号表示),并能明显表示它们之间相互关系的啮合图。
内齿轮副的过渡曲线干涉
内齿轮副在啮合过程中,由于设计不当,小齿轮的齿顶可能和内齿轮的过渡曲线相接触,这样就破坏了共轭啮合条件,这种现象称内齿轮副的过渡曲线干涉(图6-49)。不产生过渡曲线干涉的条件是:内齿轮渐开线齿廓终止点的压力角应大于或等于其齿廓工作段终止点处的压力角,于是:
为避免这种干涉,可采取增大内齿轮径向变位系数、减小齿顶高等措施。
内齿轮渐开线齿廓终止点的压力角
目前,渐开线内齿轮多用插齿刀加工,如图6-50所示插齿刀从B2点开始切制内齿轮齿廓,至B1点结束,切制出全部渐开线齿廓部分,B1点到齿根曲面之间为过渡曲面部分,其分界点B1,称内齿轮渐开线齿廓终止点,该点处压力角称终止点压力角。内齿轮渐开线齿廓终止点的压力角为:
内齿轮副的齿廓重迭干涉
内齿轮副在啮合过程中,由于两相啮齿轮齿数差过少,可能发生啮合终了,小齿轮齿顶在退出内齿轮齿槽时,与内齿轮的齿顶碰触(图6-51),这种干涉现象称内齿轮副的重迭干涉。其结果是内齿轮副不仅不能正常啮合,而且也不能实现正常安装。若小齿轮为插齿刀,则产生重迭切削干涉,内齿轮产生顶切。故重迭干涉必须避免。
重迭干涉产生的原因是一对轮齿在啮合过程中,另一对轮齿出现渐开线齿廓相交现象,显然,两齿轮顶圆出现相交以前,齿廓不出现相交现象是避免重迭干涉的条件。由图6-51b可知,其具体条件是∠ao2P≥∠Mo2P。于是可导出不发生重迭干涉的校核公式为:
由式可知影响重迭干涉的主要因素是(z2-z1),其值越小越易出现重迭干涉,(z2-z1)≥10则不出现重迭干涉。(若z2-z1较小时。为避免重迭干涉,必须增大内齿轮的径向变位系数,使啮合角a′增大。或者减小齿顶高系数。
重迭干涉,有的文献称齿顶碰角干涉,余摆线干涉;齿顶干涉,次摆线干涉,第二类干涉等。本书建议用齿廓重迭干涉这个名词较为合理。
内齿轮副轴向装配干涉
当产生重迭干涉时,内齿轮副两齿轮不能沿轴向相配安装,这种在轴向相配安装时产生的齿顶碰触现象,称轴向装配干涉。
径向干涉内齿轮副的两个相配齿轮,当齿数差过少时,当把小齿轮从内齿轮的中心位置,径向安装到啮合位置的过程中,若图6-52所示y>x,将产生齿顶碰撞现象,小齿轮无法进入啮合位置,这种现象称径向干涉。如果小齿轮是插齿刀,则要产生径向进刀顶切。
为了避免这种干涉,可采用增大压力角,减小齿顶高系数,增大齿数差z2-z1及增大内齿轮径向变位系数等措施。
见“径向进刀顶切”。
径向进刀顶切
插齿刀切削内齿轮时(图6-52),在径向进刀过程中,插齿刀的齿顶到中心线的距离y,若大于被加工的内齿轮的齿顶到中心线的距离x,则刀具齿顶和被加工内齿轮的齿顶发生碰触,产生切削干涉,齿轮齿顶被多切去一部分金属,这种现象称径向进刀顶切。不产生进刀顶切的条件是(x-y)min≥0,由该条件可导出相应的不产生径向进刀顶切的计算式。
为避免径向进刀顶切,可采取增大齿形角,减小齿顶高系数,增大变位系数(包括径向或切向),增多齿数差(z-z0)等办法。应特别注意,z-z0之值越小,越易产生径向进刀顶切,而不受齿数绝对值多少的影响。所以当z-z0之值较小时,要校核是否发生径向进刀顶切。
内齿轮副径向装配干涉
在内齿轮副产生径向干涉的情况下,不能实现径向相配安装。这种在径向安装过程中产生齿顶碰触的现象,称径向装配干涉。其实质即径向干涉。
插齿刀切制内齿轮时的顶切
插齿刀切制内齿轮时,由于齿轮齿顶圆越过刀具基圆上的啮合极点,产生顶切,此称为展成顶切(曾称范成顶切);另外由于进刀过程中,刀具齿顶可能与齿轮齿顶相遇,形成顶切,此称为径向进刀顶切。这就是插齿刀加工内齿轮时可能出现的两种顶切现象。
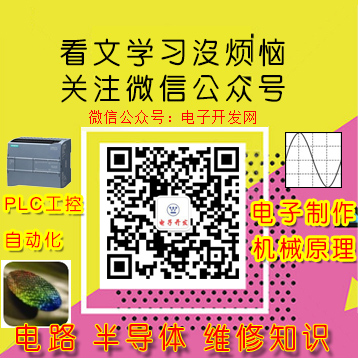