物料的混合操作是一些工厂关键的或不可缺少的一环,尤其在化工行业中,经常需要将两种或两种以上的液体按照一定的比例混合,然后再做相应的后续处理和加工。对物料混合装置的要求是设备对物料的混合质量高、生产效率和自动化程度高、适应范围广、抗恶劣工作环境等。采用PLC来控制液体搅拌机,由于其结构灵活、可靠性高、使用范围广等特点,完全满足物料混合控制工艺的要求,能大大提高对各种成分含量的有效控制,提高生产效率,因此多种物料混合的PLC控制具有广泛的应用。
多种液体按一定比例进行混合是物料混合的一种典型形式,本实例中以两种液体的混合装置的控制为例,来介绍PLC在液体混合装置控制中的应用。
一、控制工艺流程
两种液体混合装置的控制工艺流程图如图10-1所示,主要包括对混料装置的加料、混料以及出料的控制。在该控制实例中使用H、I、L3个液位传感器来检测液位,使用3个电磁阀门来分别控制液体1、液体2的进入和混合液的排出。
图10-1 液体混合装置控制工艺图
整个实例的控制流程描述如下:液面在最下方时,按下启动按钮,可进行连续混料。首先,控制液体1的阀门Q0.0,液体1流人容器。当液面上升到传感器I的位置时,关闭液体1的阀门Q0.0,打开控制液体2的阀门Q0.1。当液面上升到传感器H的位置时,控制液体2的阀门Q0.1关闭,此时搅拌电动机开始工作。搅拌电动机工作6s后,停止搅拌,混合液体阀门打开,开始放出混合液体。当液面降到传感器L的检测位置时,延时2s后,关闭混合液体阀门3Q0.2,然后再开始下一周期操作。若工作期间有停止按钮按下,则待本次混料结束后方能停止搅拌机的工作,不再进入下一周期工作。由于初始工作时,液位不一定在液面的最下方,为此需按下复位按钮,使料面液位处于最下方。
二、控制系统硬件设计
1.输入/输出信号分析
系统的输入信号:启动按钮1个,停止按钮1个,液位传感器3个,共5个输入信号,需5个输入端子。
系统的输出信号:控制进料的电磁阀2个,控制出料的电磁阀1个,电机接触器1个,共4个输出信号,需4个输出端子。
2.PLC的输入/输出分配表
编制PLC的输入/输出分配表如表10 -1所示。
表10-1 PLC的输入/输出分配表
除了上述的PLC输入输出分配表外,其他编程元件地址分配表如表10-2所示。
表10-2 其他编程元件地址分配表
3.PLC选型
根据表10-1所示的PLC输入/输出分配表,参考表2-1,考虑到留有15%的余量,本实例中选用西门子公司的S7-200系列小型PLC CPU222实现对液体混合装置的控制。
4.液体混合装置硬件接线图
根据表10-1所示的PLC输入/输出分配表,可设计如图10-2所示的PLC主机的硬件接线图。
图10-2 液体混合装置PLC控制的硬件接线图
5.液体混合装置控制逻辑图
根据液体混合装置的控制工艺流程,可设计出如图10-3所示的液体混合装置PLC控制逻辑图。
图10-3 混料罐控制逻辑图
三、系统控制程序
根据该液体混合装置的控制要求,并考虑到各个执行机构动作的转步条件,可设计其顺序功能图如图10-4所示,其对应的梯形图如图10-5所示。
图10-4 液体混合装置顺序功能图
图10-5 液体混合装置的PLC控制梯形图
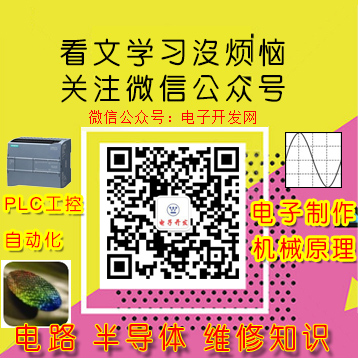