Radioisotope Thermo-electric Generator的首字母缩写,释义为放射性同位素热电式发电机。
一个有使用价值的温差发电器是由几对甚至几十对以上的温差电单体串联、串并联或并串联组成。在整个发电器中要使单体、热源、外壳三者间相互电绝缘,并且在由热源、温差电元件及附件—散热器组成的热路上有最小的热阻。
通常,温差发电器采用两种结构。一种是以热源为中心,温差电元件分列式辐射状排列的结构;另一种是将温差电元件紧压在热源一侧的平板结构。前者采用一定结构的冷端构件以后,具有极高的抗冲击振动能力,转换效率较高,但成本也较高。后者安装方便,成本较低,但热量利用率也低些。
在这两种发电器结构中温差电单体都可以采用分立元件或组合件的形式。所谓组合件就是将若干温差电单体对紧凑地排列成一个阵列,温差电元件之间电绝缘,并按一定工艺和方式焊上电极,成为一个整体,常称为温差发电组件。采用温差发电组件后发电器结构紧凑,装配容易,提高了发电器的质量比功率和热电转换效率,也增强了单体抗冲击振动的能力。但要保证每对单体都有较小的接触电阻,工艺上难度较大。
3.2.1分列元件式温差电单体结构
6-焊料片,7-冷帽,8-2N-PbTe,9-SnTe段,帽,10-硬焊片
SiGe温差电单体采用结构,如图3所示。SiGe温差电单体热端用大面积集热板(热电极)相联。冷端焊上冷电极后连接到带阴螺纹的螺栓上。热电极材料通常使用含95%Si的SiMo合金。冷电极材料一般使用钨。SiGe温差电偶和SiMo热电极上有Si3N4涂层以减小SiGe升华。温差电偶外面再绕上若干层SiO2纤维作电绝缘物。
3.2.2 温差发电组件
温差发电组件的结构类似于常规的单级温差电致冷组件,这种夹层结构示于图4。低温温差发电器较多采用碲化铋温差发电组件来组装。
温差发电组件内若干对温差电偶在电路上是串联的,在热路上是并联的。温差电元件一般呈矩形截面。碲化铋温差发电组件,通常采用铜制电极或铝制电极连接P、N型元件。
高纯氧化铝陶瓷片上有金属化互连电路。
3.2.3温差发电器的结构
3.2.3.1 低温温差发电器的结构
许多碲化铋温差发电器采用了平板结构,即将温差电元件安装在热源一侧。天使号放射性同位素温差发电器(Angel- RTG)采用了这种结构,见图5。该发电器使用碲化铋温差电组件,热面工作温度约在200℃。
4-外壳,5-输出接头,6-密封接头
图5 Angel- RTG结构示意图
3.2.3.2中温温差发电器的结构
中温温差发电器,使用最多的是PbTe基温差电材料,常用热源中心型温差电元件分列式温差发电器的结构,其典型结构示于图6。这种发电器结构已经成功地用于Snap-3、Snap-19、Snap-27等放射性同位素温差发电器中。其结构特点是热源置于发电器中心轴,温差电元件分列式辐射状排列在柱体状热源周围。在电路上温差电单体可以采用全部串联、串并联或并串联的连接方式。用弹簧-活塞-调整扣组成冷端组合体,温差电单体上加加弹簧压力负载。内部填充低热导率的绝热材料。发电器内部充氩气或混合惰性气体(氪-氢或氦-氩混合气)以抑制温差电材料升华。
1-热源,2-温差电元件,3-传热轴,4-框架,5-外壳,6-散热片
3.2.3.3 高温温差发电器的结构
通用热源放射性同位素温差发电器(GPHS-RTG),是已经成功地应用于加利略、尤利西斯、卡西尼、新视野号等空间工程的高温温差发电器,它采用了热源中心型温差电元件分列式结构,见图7。该发电器采用了前面已经介绍的可卸式锗-硅温差电单体。发电器结构和安装方式与PbTe中温发电器有很大差别。发电器装配时,将螺栓(已焊上SiGe温差电偶)插入RTG外壳带锥度的孔中,再用螺母将它拧紧在外壳上。最后温差电单体以悬臂方式支撑在外壳上。因此这种结构不需要弹簧压紧式系统。这种结构较灵活,能拆卸。螺母上施加的力矩应使螺栓略为变形,使螺栓和RTG外壳能紧密相配合,达到机械上牢固、热流畅通的目的。发电器内采用钼箔和加钼遮光石英纸交迭组成的多层箔绝热材料。
图7 GPHS-RTG的结构
如果温差发电器由温差发电组件构成,则单体对和单体条的焊接在温差发电组件的集成过程中同时完成。
温差电材料原则上可用通常的单晶体生长工艺来制备。但单晶体工艺需要精密的设备,操作复杂,成本较高。在实践中温差电材料往往采用多晶或定向多晶材料。通常,制备温差电材料的方法是粉末冶金法以及区域熔炼法。用粉末冶金法制备的温差电材料往往具有较低的热导率、较高的机械强度,但是却降低了电导率。相对而言,区域熔炼法可制备电导率较高的温差电材料,但同时也提高了材料的热导率。粉末冶金工艺,常规的有冷压法和热压法,近年来又发展了机械合金法(MA)、粉碎混合烧结(PIES)法、挤压法和放电等离子烧结法(SPS法)。通常,PbTe及SiGe合金用粉末冶金工艺制备,Bi2Te3及其合金用区域熔炼法,也可用热压工艺或挤压工艺制备。下面仅介绍粉末冶金法和区融熔炼法制备温差电材料的工艺。
3.3.1.1 配料和熔炼
配料和熔炼是所有材料制备工艺中的共有的工艺步骤。
温差电材料的配比,能够直接影响载流子浓度、迁移率、晶格参数、散射机制等物理量和状态,最终影响材料的热电性能,必须优化。各组分极少量的偏离会对温差电材料的热电性能产生极大的影响。因此,配料前精确计算各组分的重量、配料时精密称量是非常重要的。
熔炼的目的在于使各组分元素在高温时充分化合,没有组分的偏析或游离。
由于很多温差电材料的蒸气压很高,某些元素很易氧化,在熔炼时某些元素特别容易从熔炼表面逸出,以致使材料偏离配方中的比例。因此,在熔炼过程中容器必须严格密封,或者将容器抽真空后充一定压力的惰性气体,以抑制组分的逸出。也可采用能产生还原性气体的碳粉来保护。
熔炼的方法一般可采用高频感应熔炼、电阻炉熔炼等。
熔炼的工艺要素是熔炼温度、保温时间和冷却方式。选择的熔炼温度可比化合物的熔点高30~50℃。保温时间一般为30~190分钟。最后要让溶液迅速冷却。
3.3.1.2 粉末冶金法
粉末粒度大小对压制成型后的温差电材料的热电性能有一定的影响。如粒度太小,则粉末粒子互相间的接触面积十分大,将增加材料的热导率;反之,如粒度太大,则将减少材料的电导率。同时,粒度不均匀时,也会造成材料内部热电性质不均匀和机械性能的不均匀性。
温差电材料的粉碎一般采用机械粉碎法,经常采用的是捣磨法或球磨法。
成型的目的是使材料成为具有一定形状、尺寸和密度的型坯。加压使粉末成型,通过压力有可能使粒子内的很多原子在原子引力所能及的范围内互相接触,从而使粒子间产生粘附力;另外,根据粒子的形状,在加压中也有因滑动、转动等原因,其粒子之间机械的相互咬合在一起而产生维持其形状的力。也有时由于粒子表面相互摩擦,将粒子表面上的氧化膜或杂质膜破坏,而出现清洁的粒子表面,使之容易粘附。为了得到好的温差电元件,在压制成型过程中必须使密度均匀分布。
压制成型过程中所加压力的大小,依粉末种类、形状及各种条件而有很大差异。压力过大,材料上易产生裂纹、伤痕和缺陷;压力过小则使材料过于疏松,存在气泡和缺陷。
制造温差电元件时常用的粉末压制成型方法有冷压法和热压法。
封闭的刚性模具冷压法也就是常称的冷压法。其方法是将粉末放入刚性模具中,通过模冲对粉末加压,使其成型。
熔炼后的温差电材料粉末在高温下较柔软,因此热压比冷压可获得较致密和机械强度好的材料。如适当选择压力与温度,热压方法可以同时进行成形与烧结两道工序。
通常,热压必须在还原或惰性气氛中进行。一般多用
对粉末压制的温差电元件进行烧结的目的是:使温差电材料的晶粒细化,提高强度、韧性和塑性;消除应力;消除或减少材料组分和结构的不均匀性;改善材料的温差电性能。
3.3.1.4 区融熔炼工艺
使用区域熔炼法(简称区熔法)可以制备Bi2Te3及其合金的定向多晶材料。由于其晶粒有明显的取向性,通常区域熔炼法制备材料的优值比粉末冶金法高。
区熔法生长晶体,是借助于高频感应线圈加热或普通电阻加热,使材料在一个狭窄的区域内熔化,然后令熔区自下而上(或自左而右)地通过竖直(或水平)放置的粗材料进行提纯和结晶。该过程可以在真空内进行,也可以在一定还原气氛下进行。图11 是区域熔炼法示意图。
1-熔融界面,2-固化界面,3-生长的晶体,4-粗晶锭,5-安瓿移动方向,6-炉子,7-熔区,8-安瓿移动方向
为了获得定向较好的多晶体,在区熔过程中,首先要求高温区的温度高于晶体的熔点,使待区熔晶棒得以充分熔解,但必须避免熔体组分的大量挥发;而低温区的温度应低于晶体的熔点,但不能太低,避免晶体炸裂或产生大的内应力。其次在熔体生长过程中,应尽量避免或减少组分过冷现象发生。理论分析表明,发生组分过冷的临界条件为
式中,G为熔体界面处的温度梯度,V为熔区移动速率, C0为熔体中主要杂质平均浓度,m为液相线斜率,k0为杂质的分凝系数,D为杂质在熔体中的扩散系数。公式中,G和V是可以调节的工艺参量,m、c0、k0和D是晶体生长系统的物理参量。实践表明,在保证晶体不发生解理的前提下,采用适当大的温度梯度、相对小的生长速度,对避免或延迟组分过冷的出现是有利的。
3.3.2 单体连接
温差电单体的连接质量将决定温差电池的内阻和寿命,是影响温差电池质量的关键工艺。温差电单体连接工艺有焊接法、压力接触法等,常用焊接法。
电极材料、焊料中的杂质扩散入温差电材料中会使温差电材料的热电性能快速衰减。另外,如电极材料和温差电材料的热膨胀系数不匹配,在长期热循环过程中会引起接头脱落,降低温差发电器的寿命。因此,温差电元件与电极之间常进行表面处理,镀覆膨胀系数匹配、热稳定性好的过渡层壁垒。
可用来焊接温差电单体的方法有:1)火焰焊接;2)烙铁焊接;3)炉中焊接;4)感应焊接等。
采用焊接工艺连接温差电单体时,焊料成份、熔点、机械强度和焊接层所形成的接触电阻等都是直接影响温差发电器性能的重要因素。优化焊料、焊剂、焊接温度、气体保护压力等焊接工艺条件,是降低温差电单体的接触电阻,制成高性能温差发电器的关键。
炉中焊接是利用加热炉的热量加热工件的一种焊接方法。温差电单体焊接中常用电炉加热。炉中焊接法加热比较均匀,被焊工件变形小,能较好的保证设计的接头形状和尺寸公差。
温差电单体常在充满还原性气氛的焊接炉中进行焊接。还原性气氛防止了焊接时空气的入侵,同时能还原工件表面原有的氧化膜和新形成的氧化产物。惰性气氛炉中焊接时通常采用的惰性气体是氩,也有用氦。其作用是降低氧分压强。
焊接规范主要有升温速度、焊接温度、保温时间及降温速度等。
(2)焊接温度 钎焊焊接温度一般高于焊料熔点25~30℃。提高温度能减少熔化焊料的表面张力,因此改善浸润性,使焊料与焊件之间的作用加强。但温度过高会产生过烧和溶蚀等缺陷。
(5)焊接压力 压力愈大、温度愈高,温差电元件域电极紧密接触的面积也愈多。因此,在加压变形阶段,一定要设法使绝大部分表面达到紧密接触。为了防止连接构件产生过度塑性变形和蠕变以实现精密连接,有时仅在焊接开始时施加压力,或短时间提高温度以促进塑性变形。
3.3.3 温差发电组件的集成
常规温差发电组件的冷面和热面外侧是两片高纯氧化铝Al2O3陶瓷片,焊接在温差发电组件的冷面和热面与外界耦合。制作金属化陶瓷片的传统工艺方法是采用先印刷钼锰浆然后烧结的方法制备金属化层,在陶瓷片上制作金属化互连电路。温差电组件集成前预先将电极焊接在陶瓷片相应位置金属化层上。近年来,开发了敷铜板(DBP)工艺直接将铜电极烧结在陶瓷片上。温差电组件的集成应当同时保证所有接头具有一致和较低的接触电阻。
3.3.4 温差发电器的集成
温差发电器是由几十或数百对温差电单体(或者几个或数十个温差发电组件)串联或并联组成的,在整个发电器中,要使温差电单体(或温差发电组件)、热源盒、外壳三者间相互绝缘,并且使由热源、温差电元件及附件、散热器组成的热路上热阻最小。温差发电器的集成是高精度的装配过程。
温差发电器内的工作气氛必须很干净。氧、水分及其它腐蚀性成分和有害杂质的存在,都会引起温差电材料“中毒”、接头变质,加速发电器性能的衰降。有些温差电材料,如碲化铅、TAGS等,在高温时严重氧化和升华,因此,温差电发电器装配完毕、密封后,要在室温和烘烤状态下抽气,以除去水分、氧气。PbTe温差发电器则要充一定压力的惰性气体,并密封封装。SiGe温差发电器内部可以是真空状态。
温差发电器的主要性能参数包括:开路电压、输出电功率、效率、功率衰减率、重量、体积、重量比功率和可靠性等等。
载《化学和物理电源》(第二版),现代电子和信息技术丛书之一,汪继强主编,第十八章:温差发电器,国防工业出版社,2008年。
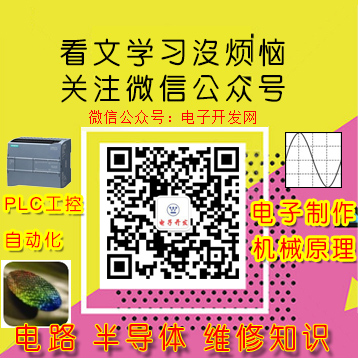