一、铝及铝合金焊接的特点及焊接性
1、 常见铝及铝合金的分类铝为银白色轻金属,纯铝的熔点为660℃,密度2.7g/cm。工业用铝合金的熔点约为560℃。按照GB/T3190-1996或GB/T16474-1996的规定,纯铝和铝合金牌号命名的基本原则是:可直接采用国际四位数字体系牌号;未命名为国际四位数字体系牌号的纯铝及其合金采用四位字符牌号。城轨事业部目前常用的铝材主要有以下三种:
①5083-H111,5表示为Al-Mg系,H111加工硬化状态:最终退火后又进行了适量加工硬化。主要用于折弯件用的板材。
②6005A-T6,6表示为Al-Mg-Si系,T6热处理状态:固溶处理后再人工时效的稳定状态。除牵引梁型材为6082之外,其余所有的型材均为6005A
③6082-T6,绝大部分板材。
二、铝合金焊接基础知识
1、定义:ISO857-1中对熔化极气体保护焊定义如下:使用丝状电极的
MIG/MAG焊接原理图
金属电弧焊,在过程中外部气源提供的气体形成的屏障将电弧和熔池与空气隔离。根据使用的保护气体类型,进一步划分为:当使用惰性气体时为熔化极惰性气体保护电弧焊(MIG)。当使用活性气体时为活性气体保护电弧焊(MAG)。
1- 母材 2-电弧 3-焊缝 4-套筒 5-保护气体 6-导电嘴 7-焊丝 8-送丝轮
原理:通过送丝马达由丝盘提供的焊丝,仅在离开焊枪前通过简短地接触导电嘴加载电流,以便电弧能在焊丝的端部和工件之间燃烧。保护气体由保护气喷嘴流出覆盖焊丝。这样保护了焊接金属,防止空气中的氧、氢、氮等的渗透。保护气体除了保护熔池之外还有其他作用,比如它确定了电弧气氛的成分,从而也影响了电弧的导电性和由此决定的焊接特性。此外它还对吸收和烧损过程以及形成的焊缝的化学成分有影响,即它由焊接冶金学方面的作用。
2 电流类型
MIG焊接通常使用直流电源焊接,电极(焊丝)连接到电源的正极,工件连接到电源的负极。
3 焊接材料
铝和铝合金焊接用焊材一般为实芯焊丝,焊材标准为EN ISO 18273。城轨事业部常用的MIG焊丝材质为5083,常见直径为Ф1.2mm,底架手工MIG焊及自动焊接使用的则为 Ф1.6mm。通常规格为7Kg/盘。
4 保护气体
DIN EN 439标准规定了MIG/MAG焊用保护气体。该标准定义了所有弧焊和弧割用的保护气体。
城轨事业部常用焊接气体为99.9999%的高纯氩(Ar),只有在底架焊接时为增加熔深采用氩氦混合气体,成分为70%氩气+750ppm氮气+剩余氦气。这是因为在氩气中添加氦气能改善电弧气氛的热传导性和保温性能,这两种影响产生了高能量的电弧和更好的电弧穿透性。
MIG焊接常用气体流量为18~20L/min。
5 焊缝坡口的形式
铝及铝合金焊接时,坡口一般采用机械方法加工,常见的坡口形式如下:
6 衬垫
MIG焊接时功率较大,熔透能力强,这样就造成焊缝金属在焊缝根部下漏,造成根部裂纹,根部成型差等缺陷。所以铝合金焊接全焊透时常需要加焊接垫板,有利于缩小接头有关尺寸,操作条件较为宽松,对操作技能可以适当降低。焊接垫板分为可移除式焊接垫板和永久性焊接垫板,可移除式焊接垫板常见材质为不锈钢或陶瓷,如下
7 焊接位置
ISO 6947中定义焊接位置如下:
PA-平焊 PB-平角焊 PC-横焊 PD-仰角焊
PE-仰焊 PF-立向上焊 PG-立向下焊
三 铝合金焊接实做
铝合金焊接因材料的特殊性,在整个焊前准备、焊接过程及焊后处理过程中有较多的注意事项及禁忌,操作人员必须注意这些事项,才能焊接出合格的焊缝。
1 焊前准备
在焊接前,必须对工件表面及型腔内部的铝屑、飞溅、毛刺、灰尘、机加工残留的切削液清理干净,然后使用异丙醇清洗液将焊缝区域清洗干净后用干净的白棉布擦干。
使用风动不锈钢钢丝轮将焊缝区域(坡口边缘两侧各20mm)氧化膜打磨掉,直到焊缝区域呈现亮白色。若清理氧化膜后12小时后并未焊接,在下次施焊前需重新打磨氧化膜。打磨过钢材的工具不得再用于打磨铝材。
检查焊缝,焊接区域不得有钢丝轮吊落的钢丝等杂物。要求全焊透的焊缝,要留有2~3mm的焊缝间隙,角焊缝装配间隙要尽量的小。
检查温湿度,作业区要求温度在5℃以上,湿度小于70%。环境不符合要求,不能进行焊接作业,当湿度超过60%而小于70%之间时,操作人员需随时关注湿度。夏季多雨季节湿度易超标,需多关注。
检查焊机状态,检查保护气体的压力、余量等,焊丝的余量。使用尖嘴钳将导电嘴拧紧
2 焊接过程
对超过8mm厚板的接头使用氧—乙炔焰预热,预热温度80~120℃。使用温度计对预热温度进行测量,切勿不使用仪器而仅评个人经验判断。
①引弧 焊枪开关按下后,焊丝开始按预设速度送丝,同时保护气体开始流出。当焊丝接触工件表面而短路,产生很大短路电流使焊丝尖端材料气化引燃电弧。此时电弧还很微弱,若送丝速度很高则电弧很可能被焊丝挤压而熄灭,这就需要二次引弧或三次引弧。现代的智能化焊机为了解决这种问题,可以编制特殊的引弧程序:在起弧的瞬间增大电流,使焊丝“过烧”,从而避免焊丝挤压微弱的电弧而造成熄弧,待电弧稳定后引弧程序终止,电流回归正常。
②焊接 引弧后,焊枪以一定姿态运行,焊枪与工件及焊接方向应保持一定的角度,但运行过程中可机动地调整。焊枪指向焊接前进方向时称为左焊法,焊枪指向反焊接方向时称为右焊法,如下图所示
若其他焊接条件相同,左焊法时熔深较小,焊道较宽较平,熔池被电弧力推向前方,操作者易观察到焊接接头位置,易掌握焊接的方向;右焊法可获得较大的熔深,焊道窄而凸起,熔池被电弧力推向后方,电弧能直接作用于母材上。铝及铝合金的焊接多采用左焊法及亚射流过渡方式。
焊接时,喷嘴下端与工件间的距离保持在8mm~15mm之间。过低易与熔池接触,过高时,弧长被拉长,保护效果变差,熔深变浅。
焊枪摆动 在焊接过程中,可以通过有规律的焊枪摆动,来提高焊缝质量,完成焊接工作,常用的四种摆动方式,其一为小幅度起伏摆动,在电流较大时,此种摆动方式可使打底焊不至烧穿,同时可加大熔深,使焊缝饱满;其二为较大幅度的在焊接方向前后摆动,适用于厚板,但焊丝摆动幅度不能超越熔池,其步骤为:前进—回拉—停留—再前进—再回拉—…,采用这种方式可以避免烧穿,同时能加大熔深;其三为划圈摆动,适用于焊接时温度过高而需避免过热,此法可将焊接热扩散,但熔深将有所降低;其四为“八字步”式摆,适用于PF位置的焊缝,这种摆动可以防止金属液下坠,也可避免烧穿。
多道焊 对较厚的工件焊接时,一道焊缝已经不能填充满焊道,这时就需要多层多道焊接。对于单面多道焊,每焊完一条焊道,需要使用钢丝刷等工具清理焊缝表面。熔覆焊道要宽而浅,以便于气体的逸出。铝合金焊接时还需严加控制层间温度为60~100℃(使用温度计测量),以防过热产生热裂纹等缺陷。对于双面多层多道焊,正面打底焊应一次焊透,在焊完一面在反面清根后,需做PT(渗透探伤)检查无裂纹后,方可进行反面打底焊接。
③熄弧 熄弧时容易产生弧坑及焊缝过热,从而产生弧坑裂纹。现代焊机一般都带有熄弧程序,可以在关闭焊枪开关后电流递减,并保持气体通送一定时间,从而时弧坑填满。操作者需要在关闭焊枪开工后继续停留一会再移开焊枪,并将余高过高处修磨平整。
铝合金焊接中,起弧端和收弧端是裂纹的高发区域,所以若焊缝中间停顿,若在接头处再次起弧,必需再次将接头打磨成斜坡状。对于重要的焊缝,如铝合金地铁车体底架的牵引梁与枕梁20mm厚板双面焊缝,需添加起弧板及收弧板,在焊缝区域外进行起弧和收弧,待焊接完成后将起弧板及收缝有无缺陷,以便返工。弧板切除。目前城轨事业部采用TPS系列焊机,都有起弧及收弧程序,操作者在焊接前需根据板厚对参数进行适当设定。焊接完成后,需对焊缝表面的黑灰等进行清理(焊接Al-Mg合金时,出现少量黑污不是缺陷),并目检焊缝质量,对有缺陷处进行标记,以便后续制定返工方案。
四 常见铝合金焊接缺陷及成因
常见缺陷 |
成因 |
焊缝金属裂纹 |
1 参数选择不合适,焊缝深宽比太大 |
2 熄弧不佳导致产生弧坑 | |
近缝区裂纹 |
1 近缝区过热 |
2 焊接热输入过大 | |
焊缝气孔 |
1 工件表面未清理干净,有氧化膜、油污、水分等 |
2 焊材表面有氧化膜、油污、或焊材受潮 | |
3 电弧太长,或套筒堵塞等导致气体保护效果欠佳 | |
4 电弧电压太高,造成电弧分散,气体保护效果变差 | |
咬边 |
1 焊接速度太快 |
2 电弧电压太高,熔池过大。 | |
3 电流过大 | |
4 电弧在熔池边缘停留时间不当 | |
5 焊枪角度不正确 | |
未熔合 |
1 工件边缘或坡口区域清理不到位 |
2 热输入不足 | |
未焊透 |
1 接头设计不合适,坡口太窄或间隙太小等 |
2 焊接技术不当,电弧应处于熔池前沿 | |
3 热输入不合适(电流太小或电压太高) | |
4 焊接速度太快 | |
飞溅过大 |
1 电弧电压过低或过高 |
2 工件表面清理不彻底 | |
3 导电嘴磨损或送丝不稳定 |
五 小结
铝合金熔化极惰性气体保护焊接,相对于普通钢材的活性气体保护焊接来说,是一种很“娇气”的焊接技术,焊前工件的表面清理、接头的装配、焊接材料、保护气体、电源、环境、焊接技术等因素有一个不到位,就很难得到满意的焊缝,操作者需严格遵守操作规程,才能焊接出漂亮的焊缝。
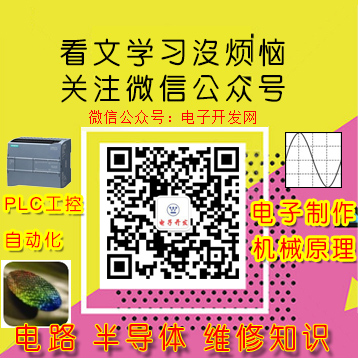